Announcing 2nd quarter winners of the Manchester Tank Find a Better Way Award
August 8, 2018
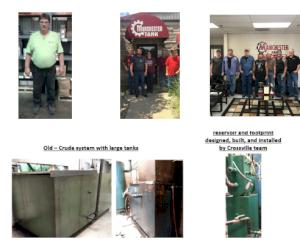
Manchester Tank is pleased to announce the following winners of the Find a Better Way team recognition award for the second quarter:
Quincy: Flux Sifter
Team members: (pictured top right) Mark Speckhart, Chance Schraeder, Nick Hankins, John Bohrer, Tom Winklejohn, Benny Lares, John Washburn, Ricky Patterson and Daniel McMullin
Project: Historically two team members manually hand sifted the sand. They found a better way to accomplish this by developing a conveyorized sifting process which enables one operator to process a one cubic yard hopper of flux/slag in 20 minutes versus two operators/two hours per hopper manually. This project results in an estimated labor savings of $17,465. It also eliminates the ergonomic hazard from hand sifting.
Bedford: Die Press
Team members: (pictured top middle) Steve Robertson, Darren George, George Johnson, Joshua Cammack, Emily Siler and Tommy Rivera
Project: This team created a die press that changed the multi-step process of rolling and putting two bends into a piece of metal to a single step to create a strap bracket. This increased efficiency and decreased production time for an order from a full day to complete to 2-3 hours to complete the full order.
Elkhart: Reduce Spend for Robot Weld Contact Tips
Team members: (pictured top left) Roger Klein
Project: Service issues with the vendor promoted Roger to solicit quotes on various parts from other vendors. In the process of evaluating new vendors, Roger negotiated a significant cost reduction for Robot Weld Contact Tips.
Crossville: (pictured bottom) New Moisture-Oil Collection System for Air Compressors
Team Members: Mike Barnett, Tony Cobb, Daniel Cole, Doug Lewis, Kevin Taylor, Jonah Tinnel and Chad York
Project: Instead of hiring an outside engineer, the team saved money by designing, building and installing a new moisture-oil collection system with a small 45-gallon reservoir to replace a very crude collection system that utilized two large holding tanks. The new system freed up floor space in the air compressor room and significantly contributed to cleaner air in the room. It is estimated that the team saved $5,000 by designing, building and installing the new system and $3,300 labor costs for manually pumping the oily wastewater to the holding tank daily before installing the new system.
Congratulations to the 2nd Quarter winners!